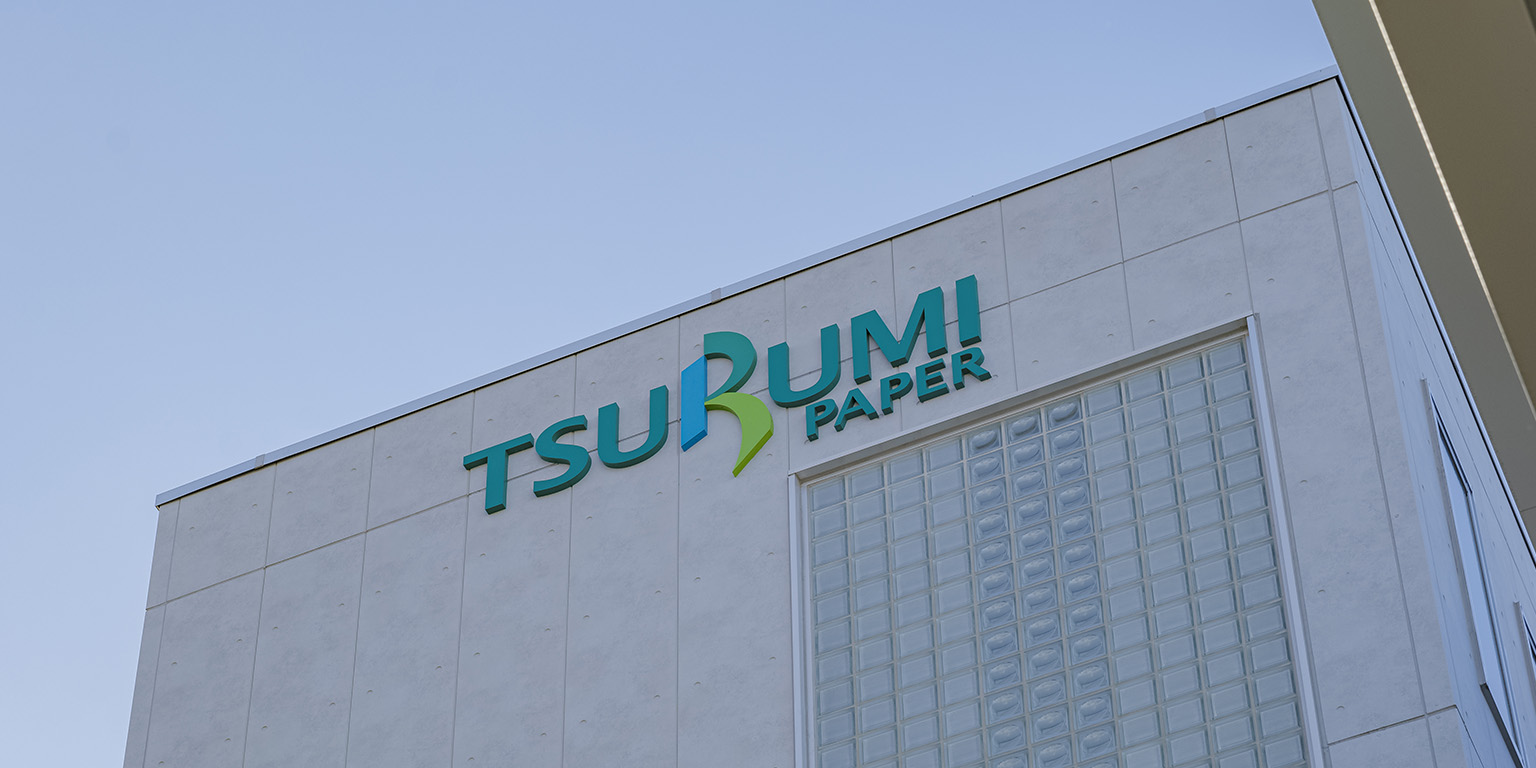
デモ機によるテスト撮影で設置場所や画角を検討
納得のプランで、品質管理の向上と生産工程の連携強化を実現
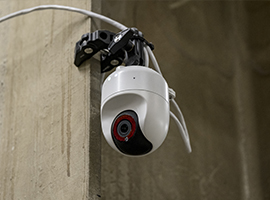
再生紙トイレットペーパーの製造・販売などを通じ、地球と共存できる循環型社会を推進する「鶴見製紙株式会社」。同社の本社工場では、品質管理や生産工程の連携強化にSafieを利活用くださっています。
(取材:2025年1月)
導入の決め手
- ビューアーのUIが優れていて操作性が良い
- クラウド型でサーバー設置が不要
- スマートフォンやタブレットで手軽に視聴できる
- 直感的に操作可能。レクチャー不要で使ってもらえる
- 柔軟にアカウント管理ができる
導入目的
- 工場内のセキュリティ
- 生産工程を映像で振り返り、不具合の原因分析を行う
- 生産工程間におけるリアルタイムな情報共有
導入した結果
- 過程の可視化により、不具合の原因を特定できる
- 原因が特定されるので、的確な改善策を取れる
- 機械エラーの映像共有により、機械メーカーとの相談がスムーズに
- 不具合のあった製品の出荷を迅速にストップでき、品質を担保
- ライブ映像で他工程の状況がわかり、足を運んで確認する負荷を軽減
- ライブ映像による作業進捗の共有で、工程間の連携が強化
INDEX
再生紙トイレットペーパーの製造・販売及び、その原料となる機密文書溶解サービスなどを通じ、持続可能な循環型社会を推進する「鶴見製紙株式会社」。埼玉県川口市にある同社の本社工場では35台のSafie(セーフィー)を導入し、品質管理の向上や生産ラインの連携強化などを実現されています。導入前のデモ機によるテスト撮影の所感と、具体的なカメラの活用方法や効果について、品質管理部の中村 俊介さんにお話を伺いました。
不具合の原因究明を目的に、生産工程を見守るカメラを導入
Safieは操作性が一番良いと感じた
──はじめに、中村さんが所属されている品質管理部についてお教えいただけますでしょうか。
中村さん:品質管理部は、生産している再生紙トイレットペーパーに不具合が生じた場合の原因究明や、改善活動などを主業務としています。同時に、品質向上を目的とした工場IT化の導入支援、生産効率アップへの取り組みなども行っています。
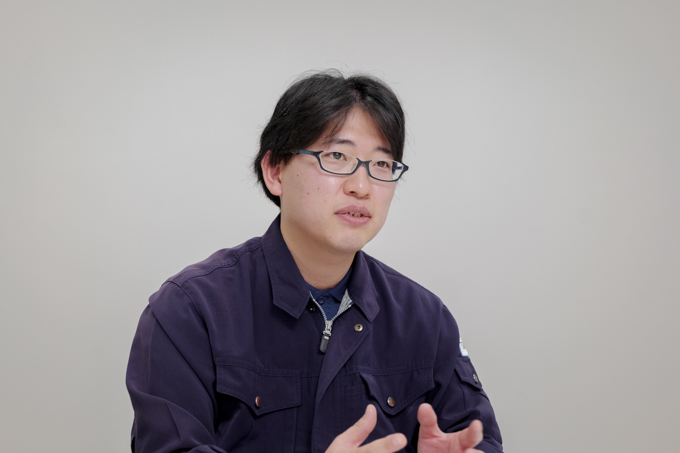
──再生紙トイレットペーパーを生産する本社工場でSafieを利活用いただいています。導入の背景にはどのような課題があったのでしょうか?
中村さん:1つは、製品の不具合の原因究明をめぐる課題です。トイレットペーパーは生鮮品などと異なり、生産してから流通に乗るまでにタイムラグがあることがほとんどです。そのため、不具合が発覚した際は生産から数ヶ月~1年単位で時間が経っていることが多く、日報などで生産工程を振り返っても詳細を確実にたどることができません。スタッフの記憶も薄れているので、可能な限りヒアリングをかけて分析を進めても、推測や仮説をもとにした対策しか立てられないことに課題を感じていました。
もう1つは、生産工程間の連携や業務効率に関する課題です。本社工場は3つのフロアに分かれていて互いの作業進捗がわからないため、滞りが生じた際は、他工程をやっている別のフロアに電話をかけたり、足を運んで様子を見たりという確認の手間が発生していました。
当社は以前から他社のセキュリティ用の防犯カメラを設置していましたが、工場内をモニタリングするカメラはありませんでした。そこで、ライブ映像や録画で生産工程を見られるカメラがあれば、工場内のセキュリティだけでなく不具合の課題も工程間の情報共有の課題も一気に解決できると考え、Safieを導入しました。
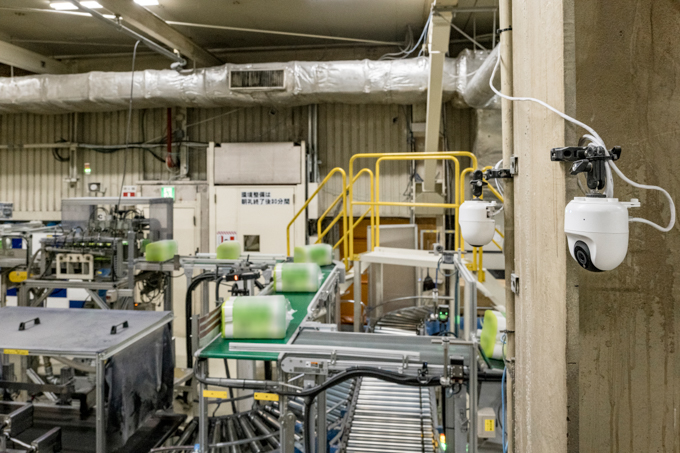
──数あるカメラの中で、Safieを選んでくださった理由をお聞かせください。
中村さん:他製品との比較検討も行いましたが、ビューアーなどの操作性、UIの使いやすさはSafieが一番優れていると感じました。クラウド型なのでわずらわしいサーバー設置や管理が不要ですし、スマートフォンやタブレットからのアクセスも容易です。また管理者目線では、フレキシブルにアカウント管理ができること、直感的に操作可能なのでレクチャー不要ですぐに使えて人事異動などに対応しやすいことも魅力でした。
コンパクトなウェアラブルカメラでお試し撮影
設置場所や画角はスクリーンショットを見ながらじっくり検討
──カメラの設置場所はどのように決めていったのでしょうか?
中村さん:前述の通り不具合発生のトレース、生産工程間の情報共有が主目的でしたから、過去の原因究明の仮説も踏まえ、ポイントになりそうなスポットを大まかに選定していきました。その後、詳細な設置場所や画角は、セーフィーの営業担当の方からお借りしたウェアラブルクラウドカメラの「Safie Pocket シリーズ(セーフィー ポケット シリーズ)」をデモ機として使用し、じっくり検討させていただきました。
──「Safie Pocket シリーズ」でのテスト撮影はいかがでしたか?
中村さん:最初にセーフィーの営業担当の方が使い方をレクチャーしてくださいましたが、あとは当社のスタッフだけで気兼ねなく試すことができました。「Safie Pocket シリーズ」はコンパクトで電源不要なため、場所を変えてテスト撮影するにはもってこいのツールでしたね。自撮り棒タイプのアタッチメント器具も貸してくださったので、いろいろな場所で画角を変えながらテスト撮影を行い、それぞれの場所、画角でスクリーンショットを撮りました。
そして、撮影したスクリーンショットでスライド資料をつくったところ、「どんな風に見えるかわかりやすい」と社内で大変好評でした。経営層とのミーティングでも実際の画像を見ながらディスカッションできるので、認識合わせがスムーズに進んで納得のいく設置プランをつくることができました。
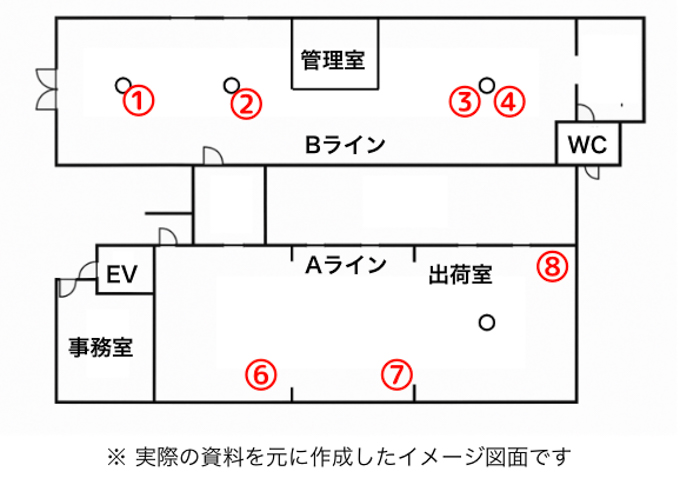
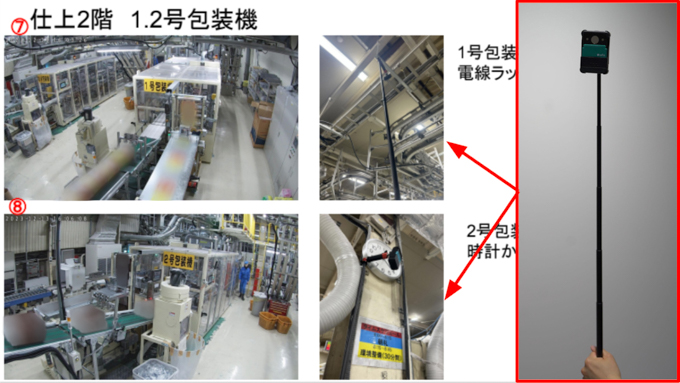
──現在の、カメラのご活用状況をお聞かせください。
中村さん:最初は9台でスモールスタートしましたが、運用する中で不具合発生のトレースに有効だと確信し、追加導入しました。その結果、現在は35台の固定カメラを工場内に設置しています。
不具合の原因究明では機械のエラー履歴を参考にしながら品質管理部でSafieの映像を見返し、どこで何が起きていたか事実確認を行います。一方、生産工程間の情報共有では、工場内に設置したデジタルサイネージに別フロアの様子を映し出し、ほかの工程の進捗をスタッフみんなが見られるようにしています。
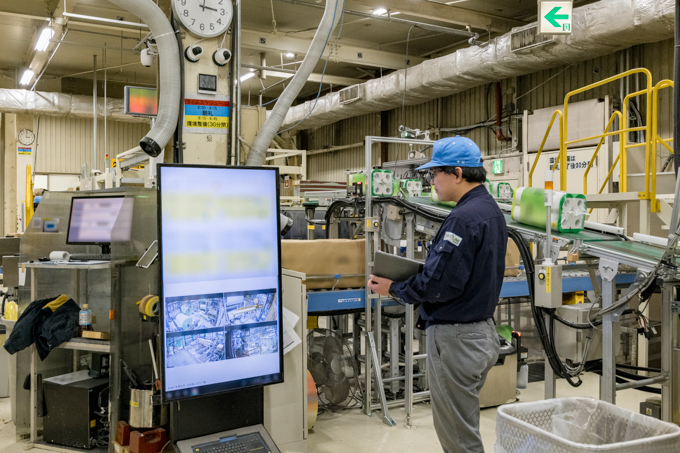
不具合品はいち早くに出荷をストップ
品質が担保され、生産工程の連携もスムーズに
──感じていらっしゃるSafieの導入効果をお教えください。
中村さん:導入のきっかけになった不具合発生の原因究明では、仮説ではなく正確な原因特定が可能になり、期待通りの大きな効果がありました。原因が機械のエラーならメーカーさんに映像で症状をご覧いただけて話が早いですし、人的エラーなら当事者と一緒にオペレーションを確認するなど、効率的な改善策が取れます。
もちろん、不具合品の出荷を未然に防げますし、エラーが起きていた時間帯が映像で可視化されるので、出荷停止の対象を過不足なく洗い出せるのもいいですね。品質管理のクオリティは間違いなく高まったと思います。
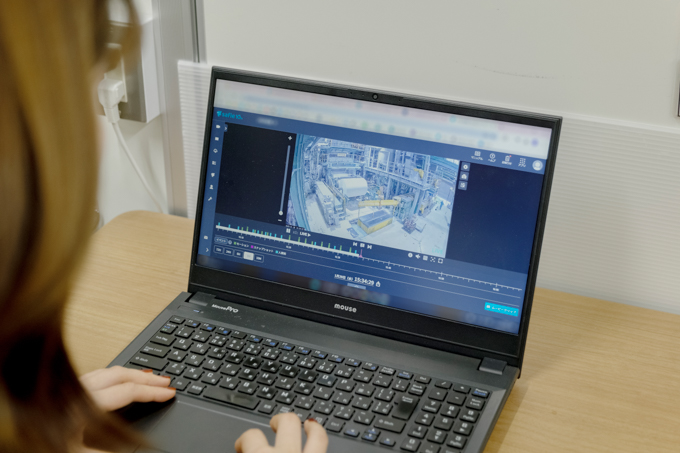
また、生産工程間の情報共有でも効果を感じています。デジタルサイネージで別フロアの作業状況がわかるので、滞りが生じても確認に行く手間が省けます。進捗状況の共有が厚くなるとコミュニケーションもスムーズになり、連携強化につながりました。当初はカメラ導入に対し懸念の声もありましたが、今ではサイネージをオフしていると「Safieが見られない」と不満の声が上がるほど浸透しています(笑)。
──最後に、映像活用における今後の展望をお聞かせください。
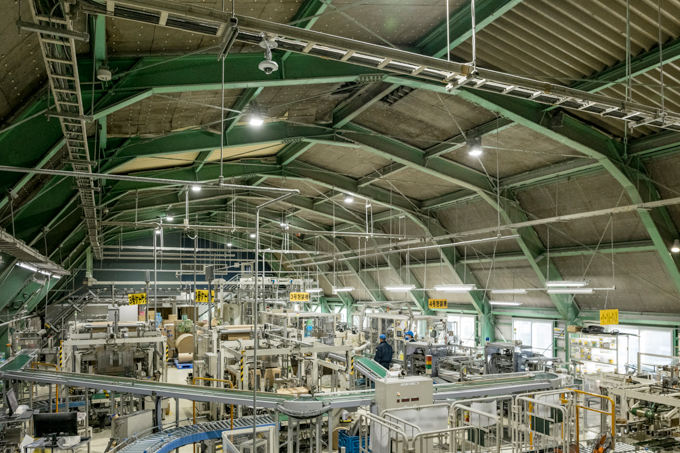
中村さん:現在、不具合発生のトレースや改善策の構築は私たち品質管理部が主導していますが、いずれは現場のスタッフ自身が原因究明や対策を行うオペレーションに移行していきたいです。すべてのスタッフが品質に対する当事者意識を高く持ち、より良い製品をお届けしたいと思っています。
※本記事に掲載している企業情報、所属及びインタビュー内容はページ公開当時のものです。
※映像の活用は事前に特定した利用目的に必要な範囲で行い、映像に写り込んだ個人を特定、追跡することは行いません。