感染症の流行や脱炭素の動きの加速など、企業を取り巻く社会環境は刻一刻と変化しています。特に製造業においては、「2022年版ものづくり白書(経済産業省)」で原材料価格の高騰などによる利益減が指摘されており、業務効率化の圧力が強まっていると言えます。
製造業における効率化の1つの方策として、「チョコ停」への対策が考えられます。工場で頻繁に起こるチョコ停は、1件あたりの損失は小さいものですが、積み上げれば影響は大きい上、放置すればドカ停につながるリスクもあります。
そこでこの記事では、チョコ停が起こる原因や影響、そしてチョコ停が解消されにくい理由を解説。チョコ停改善に向けた対策の手順とカメラを使った実際の対策事例をご紹介します。
目次
チョコ停とは?ドカ停との違いやロスとしての性質
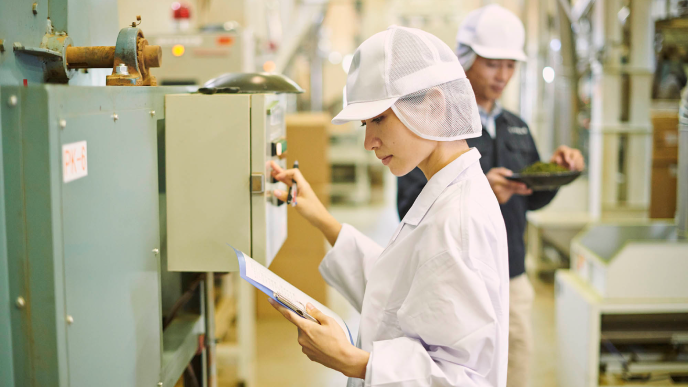
チョコ停とは、生産管理における故障のうち小規模なものを指す用語です。「チョコっと停止」を略したくだけた表現ではありますが、JIS(日本産業規格)にも掲載されている立派な生産管理用語です。JISでは、チョコ停は「小故障」の通称であるとして、「設備の部分的な停止又は設備の作用対象の不具合による停止で、短時間に回復できる故障」と定義されています(出典:JIS Z 8141 : 2001 生産管理用語 設備管理 番号6108)。
これに対し、通称ドカ停(「ドカっと停止」の略)と呼ばれる「大故障」は、同じくJISで「設備が生産ラインなどの大規模なシステムの一部となっていて,システム全体を停止に至らしめるような重大又は決定的な故障」と定義されています。
このようにチョコ停とドカ停の違いは規模の大小ですが、厳密にどの程度までがチョコ停かは決まっていません。一般的には、発生から復帰までが数分程度の軽微なトラブルがチョコ停と呼ばれます。
定義にもあるとおり、チョコ停は設備や製造過程が一時的に停止ないし空転する現象を指すため、「空転ロス」と呼ばれることもあります。製造工程には「7大ロス」と呼ばれる7種類のロスが存在し、チョコ停はその1つです。7大ロスは、まず「停止ロス」、「性能ロス」、「不良ロス」の3種類に分けられ、「空転ロス(チョコ停)」はこのうち性能ロスに分類されます。7大ロスをこの3つの分類別にまとめると、次のとおりです。
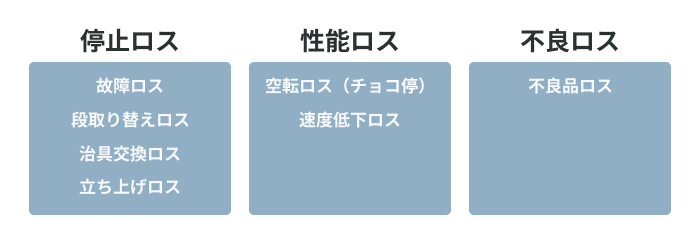
この3分類のうち、「停止ロス」と「不良品ロス」は製造ラインが稼働していない時に生じるのに対し、「性能ロス」は稼働中の製造ラインで発生するロスです。
▼おすすめクラウド録画カメラ
チョコ停が起こる主な原因
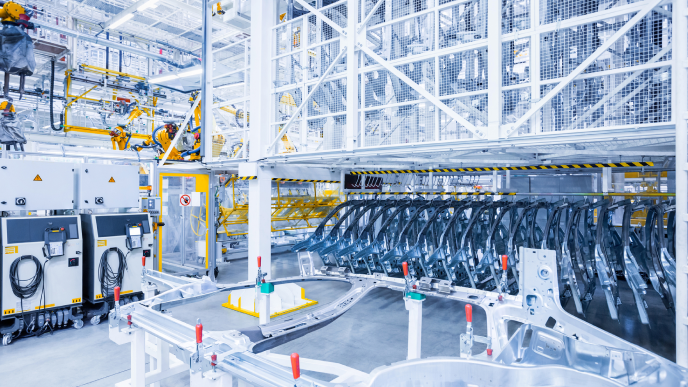
チョコ停が起こる原因は様々ですが、主に次のようなものが挙げられます。
ラインの詰まりや引っかかり
製造ラインでは、何をどのくらいの数、どのくらいの速度で流すかを適切に設計できていないと、詰まりや引っかかりが発生しやすくなります。つまり、ラインバランスの悪さがチョコ停の主な原因の1つと言えます。
材料の品質のばらつき
加工品の製造においては、ある工程で加工された材料の品質にばらつきがあると、次の工程でチョコ停が起きる可能性が高まります。不良品が選別されてラインを流れない仕組みが求められます。
センサーのエラー
ラインを流れる材料などはセンサーでチェックされますが、センサーの認識精度は経年劣化や環境上の理由で下がることがあります。これが理由でセンサーの読み取りエラーが発生すると、チョコ停に繋がります。
設備のメンテナンス不足、清掃不足
定期的な設備のメンテナンス不足も、チョコ停の主要因の1つです。例えば、金属や木材の加工プロセスでは削りくずなどが発生しますが、清掃が不十分であると機械が正常に動作しなくなり、設備が停止することがあります。このようにメンテナンス不足に起因する設備停止のうち、設備の修理なしで復旧可能なものはチョコ停とされます。
▼おすすめクラウド録画カメラ
チョコ停の影響とチョコ停が解消されにくい理由
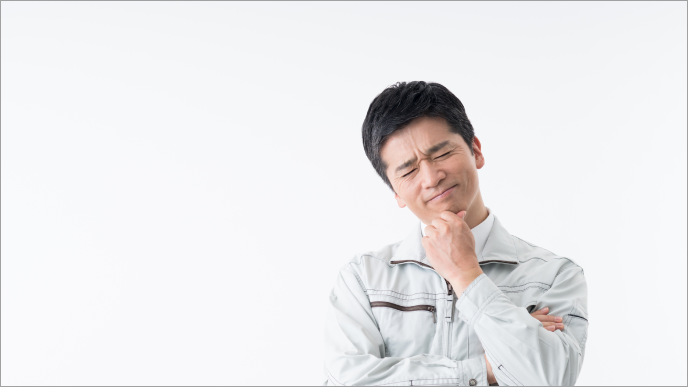
このようにチョコ停は軽微な設備停止であり、多くの製造現場では日常茶飯事です。復旧までの時間は数十秒から数分程度であるため、1度のチョコ停で大きな損害が生まれるわけではありません。ですが、毎日何度も起きるチョコ停の損害を積み上げて考えると、その影響は無視できない規模になるのではないでしょうか。
チョコ停の影響は、金銭的な損失だけにとどまりません。チョコ停は製造工程全体の稼働率に影響するため、何度も続けば製造に大きな遅れが出て、納期に間に合わなくなってしまう危険性があります。また、例えばチョコ停が成型プロセス上で起きた場合、成型不良で廃棄処分となる製品が発生します。このように、チョコ停は製品の品質低下や不良品増加の原因でもあります。
さらに、チョコ停からの復旧は作業員が手作業で行いますので、その際に問題が起きる可能性も見過ごせません。作業員がラインに立ち入った際に異物が混入する可能性など、復旧作業が製品の品質低下を招いてしまうケースも考えられます。当然ながら作業員は設備を停止させた状態で対処しますが、チョコ停の原因を解消した途端に、残圧で設備が動いてしまう場合があります。これが原因で作業員が大けがを負う可能性も考えられるため、チョコ停は安全上のリスクであるとも言えます。
こうした直接的なリスクもさることながら、製造現場でチョコ停が頻発している場合、ドカ停へと発展するリスクが潜んでいると言えます。先に解説したように、チョコ停の原因の1つは設備のメンテナンス不足ですが、その状況を放っておくことで機械に過剰な負荷がかかれば、大きな故障が発生する可能性も排除できません。ドカ停が起きればその影響は甚大になりかねないため、チョコ停を軽視せずにしっかりと対処をすることが望まれます。
その一方、上で触れた7大ロスのうちチョコ停は工程上で想定されていないロスであり、かつ停止時間が短いために、最も顕在化しにくいロスと言えます。チョコ停は突発的に起きるため、発生するたびに現場作業員が対応して原因を取り除き、正常な状態に戻すのが一般的な対処方法です。しかし、このように作業員が都度対応しているだけでは、正確な記録が残りづらく、抜本的な対策につながりません。
これでは本当の意味でチョコ停対策をしているとは言えず、損害が拡大するリスクも放置されたままです。このような場当たり的な対処のあり方が、製造現場でチョコ停が解消されにくい理由と言えるでしょう。
チョコ停を改善するために求められる対策
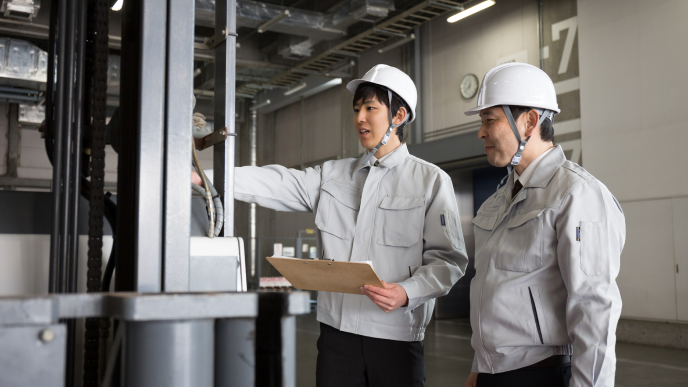
それでは、チョコ停を改善するためにはどんな対策が求められるのでしょうか。ここでは、効果的なチョコ停対策を講じるためのプロセスを、3段階に分けて解説していきます。
1.チョコ停によるロスの可視化(ワークサンプリング)
顕在化しにくいチョコ停に対して適切な対策を講じるためには、まずチョコ停によるロスを可視化することが重要です。そこで、「ワークサンプリング」と呼ばれる調査でロスを数値化します。
ワークサンプリングとは、トラブルの発生原因や従業員の動作、機械の稼働状況などを細かく確認し、何にどのくらいの時間がかかったかを調べることを言い、「稼働分析法」とも呼ばれます。トラブル発生時だけでなく、工場の作業や生産の状況を調査する目的でも行われます。具体的には、設備の稼働状況を「稼働」と「非稼働」に分けた上で、非稼働の状態を7大ロスに分類してサンプリングしていきます。まずは、こうしてチョコ停によって失われている時間を明確化しましょう。
チョコ停を原因とする稼働率の低下を数値化したい場合は、次の式で2種類の稼働率を計算してみてください。この2つの差分が、チョコ停による稼働率の低下です。
- チョコ停がない場合の稼働率 = 稼働時間 / 操業時間
- チョコ停を加味した稼働率 = 稼働時間 / (操業時間+チョコ停時間)
なお、操業時間とは1日のうちに設備が稼動しうる時間です。これに対し、稼働時間とは実際に設備が稼働していた時間であり、操業時間から計画停止時間と停止ロス時間を引いたものです。
2.チョコ停の原因の調査と重大原因の抽出
ロスの可視化ができたら、ワークサンプリングで明らかになったチョコ停の原因(チョコ停が発生している工程)を書き出した表を作成し、それぞれの原因で起こるチョコ停の回数を作業員に記録してもらいましょう。
こうして原因別にチョコ停の発生回数を比較し、特に頻発にチョコ停を引き起こしている原因を抽出することで、効率的にチョコ停対策を講じることができます。
3.対策の実施と評価
実際にどのチョコ停原因に対して対策を実施するかを判断する際は、チョコ停を改善することによって得られる経済的効果を試算するとよいでしょう。まずは、次のとおりにチョコ停による損失額を計算します。
1日あたりのチョコ停の損失金額 =(時間当たりの製造数 × 製品の単価)× 1時間あたりのチョコ停時間 × 1日の操業時間
表を使った調査で特定されたチョコ停の重大原因のそれぞれについて、1日のチョコ停時間全体に占める割合を算出してみましょう。それを上記の損失金額に掛けて導かれた数字が、それぞれの原因を解決した場合の経済効果となります。
また、実際に対策を実行した後は、きちんと効果を検証することが重要です。もし対策後にチョコ停の発生件数が想定ほど減っていなかった場合は、対策が有効でなかったと考えられます。期待した経済効果が実現しないことになってしまうため、さらなる調査を行って原因究明に努める必要がありそうです。
チョコ停対策のプロセスは上のとおりですが、基本的なチョコ停対策として、設備の保全は必須と言えます。
保全活動には、設備の不具合の兆候を検知して故障を未然に防ぐ「予知保全」、そして設備を計画的に点検し、必要に応じて修理や取替えを行う「予防保全」があります。予防保全には、作業員による日常的な清掃や点検の他、劣化診断技術を使った定期検査、さらに劣化部分の補修や整備といった取り組みが含まれます。
関係する部署とも連携しつつ、日ごろから保全活動を怠らないようにすることが、チョコ停改善の第一歩と言えるでしょう。
▼おすすめクラウド録画カメラ
チョコ停対策事例:カメラ導入で80万円のロス削減効果も
ここまでで見てきたように、チョコ停の原因究明のためには、まず正確なデータが欠かせません。ご紹介したワークサンプリングや表を使った原因調査は人員を割いて行う必要がありますが、例えばカメラを使えば、より効率的にデータを集めることができます。そこで、この記事の締めくくりとして、カメラを使ったチョコ停対策の事例を2つご紹介します。
事例1:株式会社MonotaRO様
ECサイト「モノタロウ」を運営する株式会社MonotaRO様は、チョコ停の原因を探るためにクラウドカメラを活用しています。
株式会社MonotaRO様の笠間ディストリビューションセンターでは、定点カメラも導入されていますが、チョコ停は発生時間も場所も様々です。そこで、トラブルが起きた箇所に、電源不要でコンパクトな別のクラウドカメラを設置し、次にチョコ停が発生した際に映像に捉えることによって、原因を探っています。
これまでにカメラのおかげで原因が突き止められたトラブルは20件ほどあり、直接的に削減されたロスを金額に換算しただけでも、その効果は約80万円にのぼるといいます。これは、再発を防止できたトラブルでラインが止まっていた時間の作業ロスを、影響を受けた従業員の人件費に換算した数値であり、原因を突き止められなかった場合に引き続き発生していたであろう作業ロスも考慮すれば、効果はさらに大きくなります。
\株式会社MonotaRO様活用事例はこちら/
事例2:トーヨーカネツ株式会社様
物流ソリューション事業などを展開するトーヨーカネツ株式会社様は、顧客の物流センターに納品したシステムのうちチョコ停の原因になりそうなところにクラウドカメラを設置しています。
カメラを導入したことで、トラブル発生時に現地に急行したり人が張り付いたりする必要がなくなり、人的リソースを有効活用できるようになったといいます。さらに、映像はありのままの事実で人の主観によるバイアスがかかっていないため、的確かつスピーディーな事実確認と原因究明を実現できているとの声も上がっています。
\トーヨーカネツ株式会社様活用事例はこちら/
これらの事例からは、既存の設備に変更を加えることなく簡単に設置や移動ができ、どこからでも映像を確認できるというクラウドカメラの利点が、効率的なチョコ停の原因究明に大いに役立っていると言えそうです。
終わりに
この記事では、チョコ停が起こる様々な原因やチョコ停が起きた場合の多方面への影響について詳しく解説しました。最後に紹介した2つの企業の具体的な対策事例では、クラウドカメラがチョコ停の原因究明に大いに役立つことがおわかりいただけたのではないでしょうか。
株式会社MonotaRO様がチョコ停の原因究明のために導入したSafie Pocket 2は、作業員が身に着けることもできるコンパクトなウェアラブルカメラで、クラウドカメラの中でも特に移動性に優れています。株式会社MonotaRO様は、このカメラをたったの2台導入しただけで、次々とチョコ停の原因究明を実現しています。
- 製造業界向けクラウドカメラ活用ガイド
- 製造業界におけるクラウドカメラの活用方法と導入事例をご紹介しています。
※顧客や従業員、その他の生活者など人が写り込む画角での防犯カメラの設置・運用開始には、個人情報保護法等の関係法令の遵守に加え、写り込む人々、写り込む可能性のある人々のプライバシーへの配慮が求められます。防犯カメラとプライバシーの関係については、こちらの記事で詳しく解説しています。
▶「防犯カメラとプライバシーの関係。事業者が注意すべき設置のポイント」
※カメラの設置に際しては、利用目的の通知を適切に行うとともに、映像の目的外利用を決して行わないことが求められます。適切なデータの取り扱いについては、こちらの記事で詳しく解説しています。
▶「カメラ画像の取り扱いについて」
※ セーフィーは「セーフィー データ憲章」に基づき、カメラの利用目的別通知の必要性から、設置事業者への依頼や運用整備を逐次行っております。
※当社は、本ウェブサイトの正確性、完全性、的確性、信頼性等につきまして細心の注意を払っておりますが、いかなる保証をするものではありません。そのため、当社は本ウェブサイトまたは本ウェブサイト掲載の情報の利用によって利用者等に何らかの損害が発生したとしても、かかる損害については一切の責任を負いません。