自動車部品製造業を営む三井屋工業さま(セレンディップ・ホールディングス連結子会社)でのスマートファクトリー構築事例をもとに、不良率や可動率(べきどうりつ)、離職率の改善に取り組まれた製造マネジメントの変革についてご紹介。
(※2023年2月8日のセレンディップ・ホールディングス株式会社さま、ウイングアーク1st株式会社さまおよびセーフィーで共催した【中堅中小企業の製造業DX】と題したセッションより、内容と資料を抜粋しています)
目次
製造業を取りまく環境の変化
「過去の経験」や「計画」だけでは、もう将来予測ができない時代になったと認識する必要がある
現代は「VUCA」時代に突入したと言われていますが、新型コロナウイルス感染症の流行によって、その不確実さを痛感することも多かったのではないでしょうか。従来通用した方法がこれから先はまったく通用しない時代になっています。
VUCA(ブーカ)とは? …Volatility(変動性)・Uncertainly(不確実性)・Complexity(複雑性)・Ambiguity(曖昧性)の頭文字を取ったもの
自動車部品の製造現場でも、これまでは考えられなかったことが当たり前に起こるようになっています。たとえば、これまでだと明日、明後日、来月と生産はおおよそ決まっていて、変動もありませんでした。ところが、コロナ禍になってからは、明日生産をするかどうかもわからないというように、この2年ほどで世界のゲームのルールが変わってしまった。
経営者の方々は「今のこの状況をなんとか耐え忍びます」と言われることが多いのですが、実はこの現状認識こそが間違いなのではないでしょうか。
結局のところ、「過去の経験」や「計画」だけでは、もう将来予測ができない時代になってきている。つまり、待てばまた元に戻るという前提ではなく、今の状況にフィットしたやり方で経営をしていく必要があるのです。
求められる「企業変革力」
経済産業省の「ものづくり白書」には、こうした不確実性の高い状況には「企業変革力(ダイナミック・ケイパビリティ)」と呼ばれる考えで対処するべきだ、と書かれています。
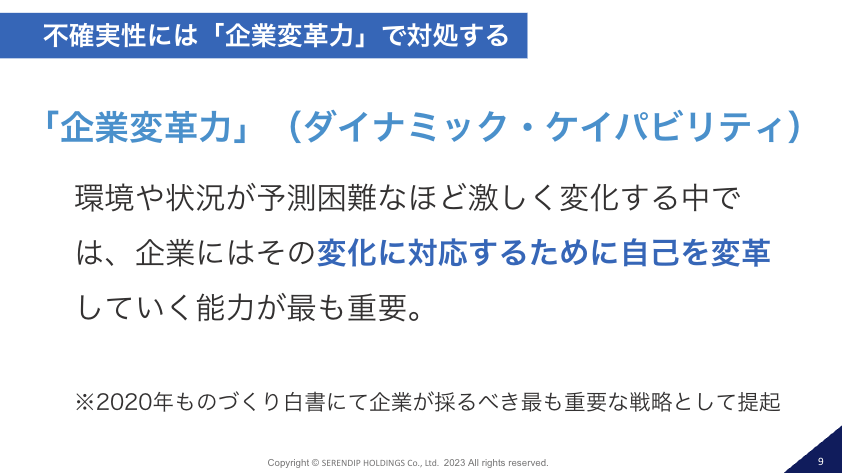
企業にとっては、環境や状況の変化に対応するために自己を変革していく能力が重要になり、そのために必要なのがDXです。
DXというと、どうしても「デジタル」の部分が先行しがちですが、「デジタル」はあくまで手段に過ぎません。肝心なのは「トランスフォーメーション=変革をする」という部分です。
三井屋工業さまの課題
悪循環の中にあった製造現場
今回DXの事例としてご紹介する三井屋工業さまが抱えていた課題は、大きく分けて3つありました。
①:「見えない・見ようとしない・見えるのに時間がかかる」
例えば不良品数について、当時は現場で紙の作業日誌を運用していました。現場からの報告では不良率がだいたい2%となっていたところ、財務諸表を分析して不良率を計算すると4%。
数字が乖離していた原因は、作業日誌の集計ミスだったり、書き漏れ、書き間違い、見落としなどでした。作業日誌の運用を毎日継続的に指導すると、4か月ほどかかりましたが実態値も4%程度を示すようになりました。
②:「コミュニケーションエラー」
上司と部下の間でも、部署間でも、あらゆるところでコミュニケーションエラーがありました。
③:「やらない・行動が遅い・やったもん負け」
行動計画が実行されていない又は大きく遅れていたり、やったもん負け(やると仕事だけが増えて損をするのでやらない)の空気があったりしました。
3つの課題が招いた結果
その結果、生産準備がきちんとできていないなかで作業が始まるため、まず不良率が悪化していきます。不良率が悪化しても、その日に出すべき良品の数は揃えなければならないので、残業して補うことになり、生産性が下がります。
残業代や不良のコストで収益が悪化し、それを見た従業員が会社の経営状態に不安を感じて離職。そして、離職によって現場の力量が落ち、また不良率が悪化するという悪循環が続いていました。
日報の電子化から始まった正のスパイラル
当初4%あった不良率がなんと平均0.4%程度に?
こうした状況のなか、経営施策としての取り組みの1つの柱が、日報の電子化、つまりデジタル化でした。電子日報というソリューションを自分たちで作って使い始めたんですね。こちら、昨年からは社外からも要望をいただくことが多くなり、現場の見える化ツール「HiConnex」として外販もしています。
「HiConnex」を導入したらこうなるというよりも、「現場が見えるようになるとどうなるか」を説明していきたいと思います。
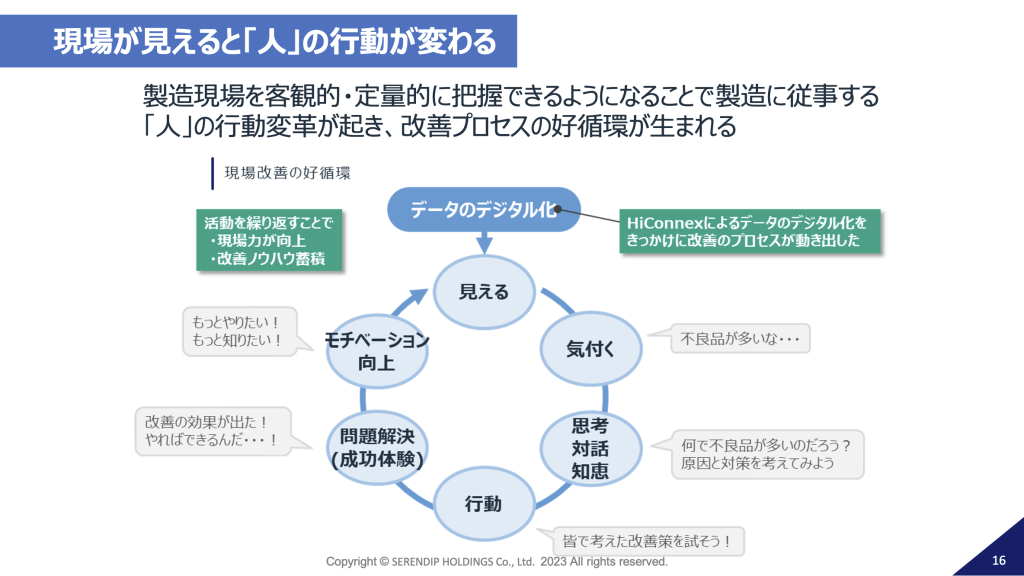
現場が見えると、結果的に「人」の行動が変わります。そのプロセスとして、実態が見えてくると、人がそれに気づく。作業をしている本人だけでなく、上司や他部署、たとえば保全や生産技術、品質管理などの部門のメンバーも気づきます。
そうなると担当者は放置できなくなり、なんとかしようと考えるようになります。誰もが同じ現場をデータで見ているため、対話が始まり、知恵が出て、実際にやってみようということで改善が始まります。
改善した効果も見えるので、成功体験によってモチベーションが上がり、さらに次の改善へ、という流れで、どんどん行動が変わっていくのです。このように、先ほど触れた悪循環とは反対の正のスパイラルが回り、自律的に現場の改善が始まっていきました。
その結果、三井屋工業さまの場合、当初4%ほどあった不良率が今では平均0.4%程度になっています。工場ごとで見れば0%の月も出てきているので、これは大きな変化です。
離職率も当初9%ほどだったものが今では1%を切っており、こちらにも大きな改善が見られています。
“ゆるい”DXで異常とも言える数値改善結果が
東北にスマートファクトリーを開設した狙い
このようにデジタルでの色々な取り組みを本社の工場で行っているなかで、山形県の米沢にスマートファクトリーを立ち上げました。
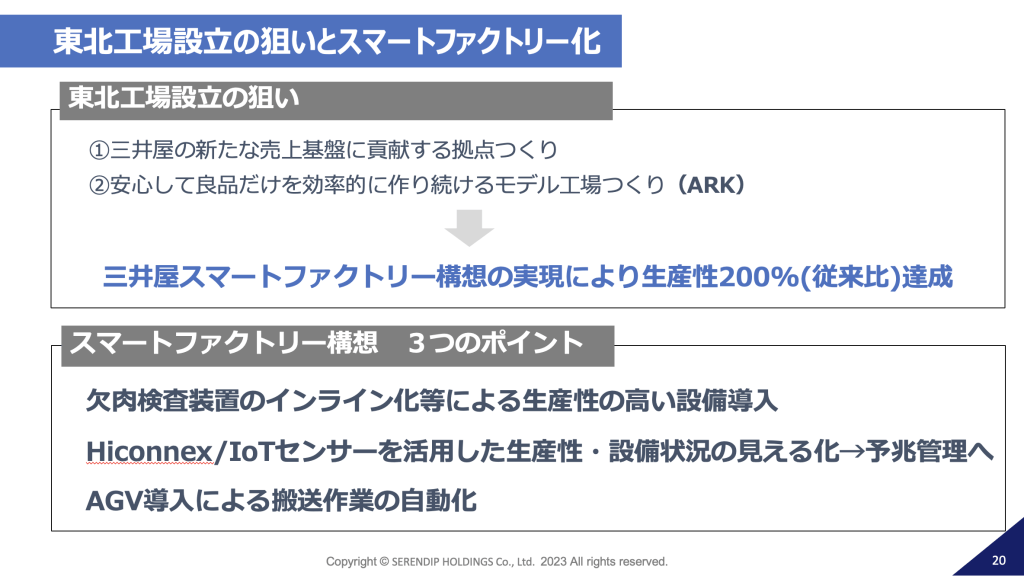
この企画自体も自社で考案していて、その責任者も特にITの専門家やDXの経験者ではありませんでした。ゼロから、お金もあまりかけずに実践したこの取り組みは、中堅企業でも十分できることだと思っています。
“ゆるい”DXで起こった劇的な変化とは?
スマートファクトリーでのDXの取り組みの鍵として、「できる範囲でゆるくやろう」という考えがありました。
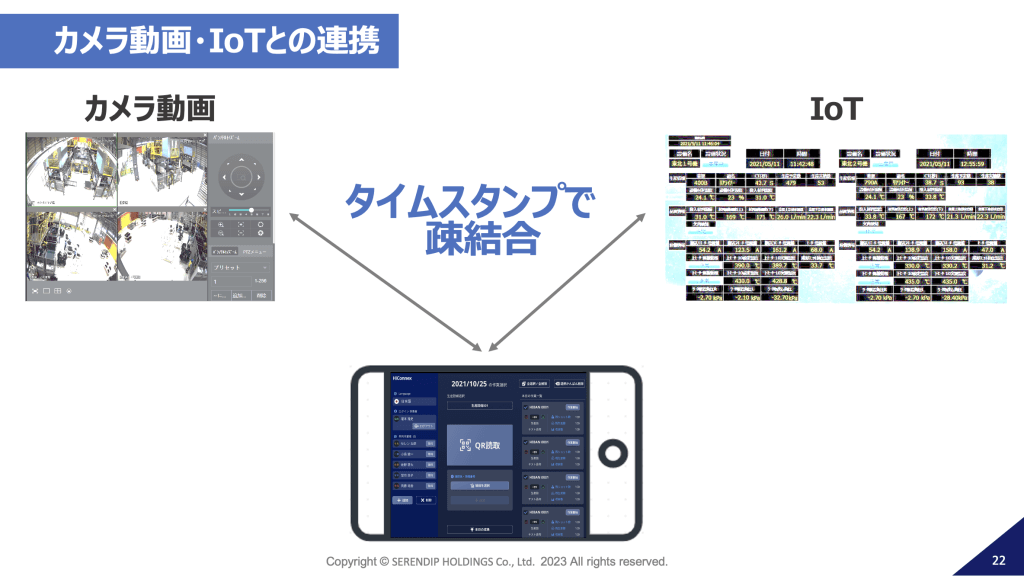
スマートファクトリーでは、「HiConnex」をインストールしたタブレットを置いて、作業者がボタンを押すだけで、何時何分から何時何分までどの品番を生産したのかを記録することにしました。機械が停止するというような異常が起きた場合も、ボタンを押して、何時何分何秒に機械が停止したという情報を記録していきます。
これによって異常が起こった時間帯が記録されるので、現場のメンバーは、その時間帯のカメラ映像と機械の状態をデータで確認します。
機械が停止したときの動画を見ると、これまで仮説ベースだった原因を特定できます。設備系データからも、たとえばヒーターの温度が異常だったことが確認できれば、どのヒーターを修理すべきかがわかります。
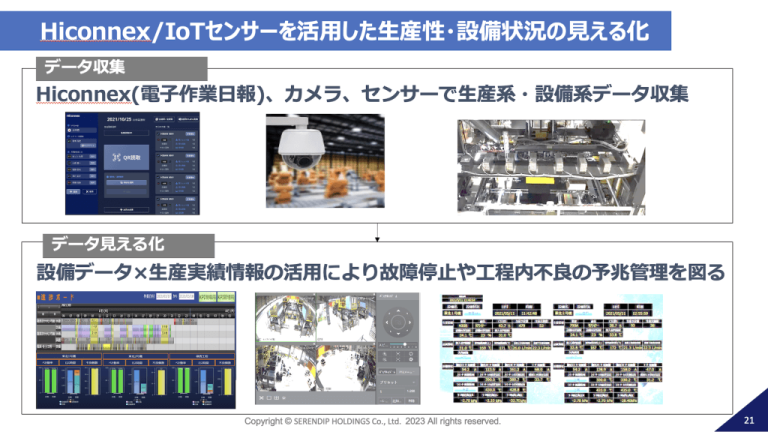
原因特定にかかる時間を大幅に短縮できた上、精度も劇的に上がりました。結果、本社の工場では可動率(べきどうりつ)が平均85%程度のところ、東北のこの工場では95%を超えており、場合によっては99%と、異常とも言える数字も出ています。
不良率も本社の半分近い数字で、ゼロが出ることもあります。先ほど説明したように、別個のデータをタイムスタンプで疎結合するだけでも、これだけの変化を生み出せるのです。
過去のものづくりの考え方を捨てる
スマートファクトリーでは、「不良0」や「設備停止時間0」といった目標を掲げました。
たとえば不良を半分にする、あるいは設備停止時間を20%削減するという目標であれば、アナログでも改善を繰り返していけば達成可能な、いわば延長戦の世界になってしまいます。
一方で、ゼロというのは、これまでのやり方・考え方では達成できないもの。エンジニア目線で見ると0というのは異質な数字であり、不可能に近い感覚ですが、この目標を掲げることで過去のものづくりの考え方を捨てなければいけない、というスイッチが入ったと思います。
過去にとらわれず、新しいアイデアで、使える部分でデジタルも使って、工程や工法すら変えようという取り組みもしています。
このようなマインドセットにするために、特に経営陣がやらなければならない一番大事な部分が、このように「飛んだ」目標を設定するということではないでしょうか。
記事は後編へ続きます。
(製品情報)
・人の行動を変革する「HiConnex」
・データを集約・可視化、アクションにつなげる「MotionBoard」
・クラウド録画サービス「Safie」
※顧客や従業員、その他の生活者など人が写り込む画角での防犯カメラの設置・運用開始には、個人情報保護法等の関係法令の遵守に加え、写り込む人々、写り込む可能性のある人々のプライバシーへの配慮が求められます。防犯カメラとプライバシーの関係については、こちらの記事で詳しく解説しています。
▶「防犯カメラとプライバシーの関係。事業者が注意すべき設置のポイント」
※カメラの設置に際しては、利用目的の通知を適切に行うとともに、映像の目的外利用を決して行わないことが求められます。適切なデータの取り扱いについては、こちらの記事で詳しく解説しています。
▶「カメラ画像の取り扱いについて」
※ セーフィーは「セーフィー データ憲章」に基づき、カメラの利用目的別通知の必要性から、設置事業者への依頼や運用整備を逐次行っております。
※当社は、本ウェブサイトの正確性、完全性、的確性、信頼性等につきまして細心の注意を払っておりますが、いかなる保証をするものではありません。そのため、当社は本ウェブサイトまたは本ウェブサイト掲載の情報の利用によって利用者等に何らかの損害が発生したとしても、かかる損害については一切の責任を負いません。